worriedman
Well-Known Member
Been wanting something different, here we go. Had Kim Monothy of Chase Mountain Custom (chasemountaincustom.com)do me a stub barrel in .25X.307AI, basically a rimmed .308 necked down to .25 caliber, Pac Nor barrel heavy varmint profile turned to match the donor stub.
Cases. .307 Win. parent, fire formed .25X.307, and .243 for comparison.
The diameter required him to fit and work a new walnut forearm, pillar bedded and free floated.
I had acquired a new Pro Hunter thumb hole composite stock, so I decided to fit a forearm to match. Standard 26" rifle forearms are too thin, so I picked up a 12 ga. forearm and went to work.
Used my old 1" pipe that I lap scope rings with, diameter close enough to the barrel to make it work. Deepened the channel and evened it all out.
Wanted to put aluminum pillars in to space the forearm off the barrel, so I got the bright idea to tap the screw holes in the forearm and thread the stand offs.
First problem, how to hold the stand offs for threading? I drilled a 5/16 bolt and tapped it to 10X24tpi.
Set the stand off on it and threaded 3/8"X24tpi.
Got a "Q" bit to relieve the existing screw holes in the forearm, and tapped them to the same thread pattern.
Slotted the stand offs with a dremel tool to give me "screw driver" bite.
Put epoxy on the threads, set the studs a little high, and used the bar to "cove" the tops to match the barrel profile.
Ran out of "daylight" last night. will finish up by building dams of modeling clay in the hollow spaces to surround the pillars and fill with JB weld, clamp to the barrel to form a shoulder with the pillars in the center.
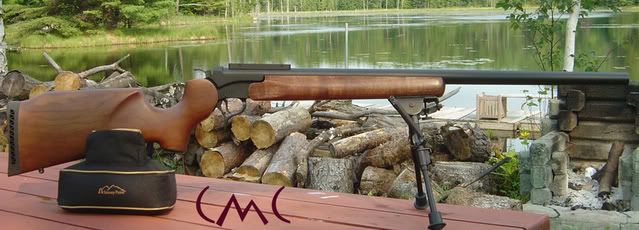
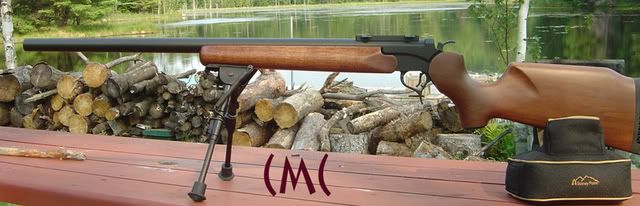
Cases. .307 Win. parent, fire formed .25X.307, and .243 for comparison.
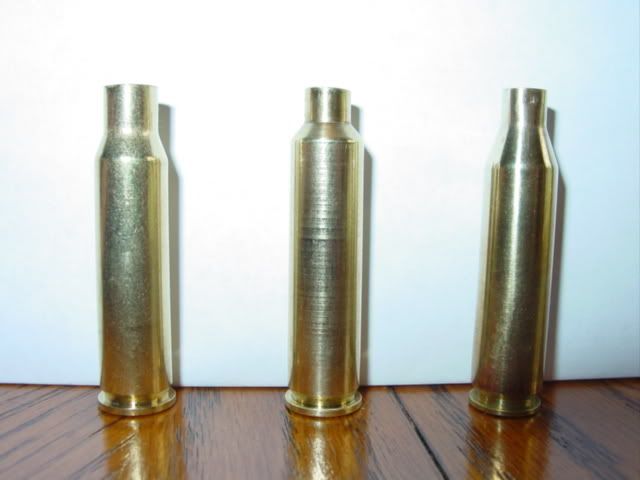
The diameter required him to fit and work a new walnut forearm, pillar bedded and free floated.
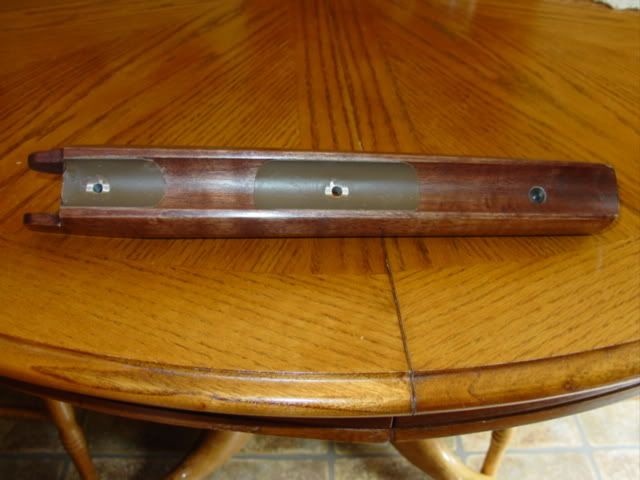
I had acquired a new Pro Hunter thumb hole composite stock, so I decided to fit a forearm to match. Standard 26" rifle forearms are too thin, so I picked up a 12 ga. forearm and went to work.
Used my old 1" pipe that I lap scope rings with, diameter close enough to the barrel to make it work. Deepened the channel and evened it all out.
Wanted to put aluminum pillars in to space the forearm off the barrel, so I got the bright idea to tap the screw holes in the forearm and thread the stand offs.
First problem, how to hold the stand offs for threading? I drilled a 5/16 bolt and tapped it to 10X24tpi.
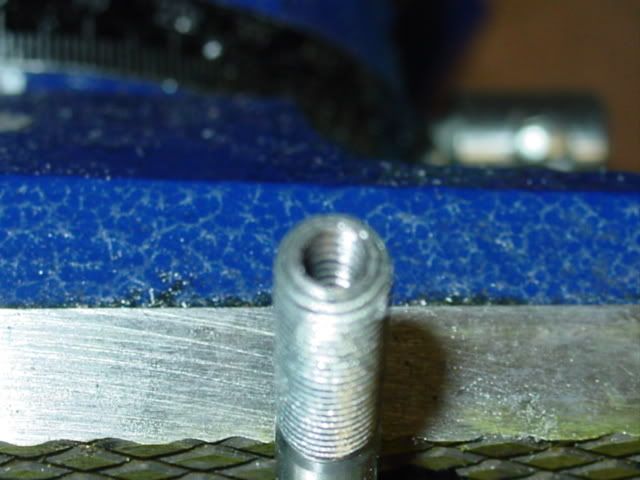
Set the stand off on it and threaded 3/8"X24tpi.
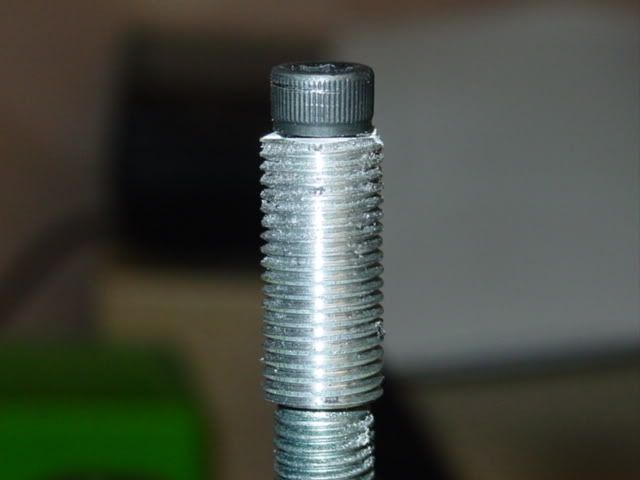
Got a "Q" bit to relieve the existing screw holes in the forearm, and tapped them to the same thread pattern.
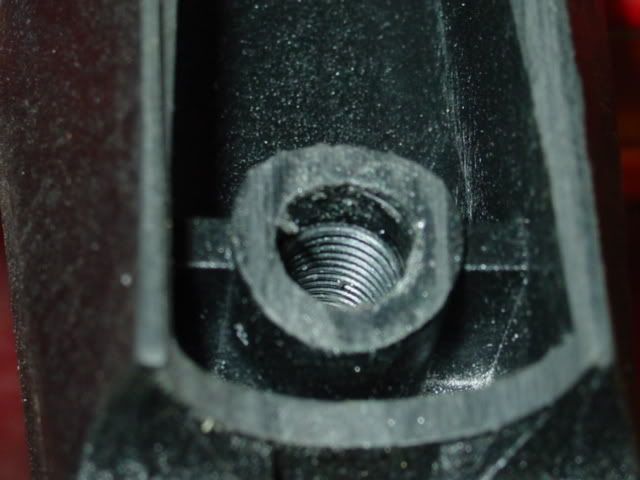
Slotted the stand offs with a dremel tool to give me "screw driver" bite.
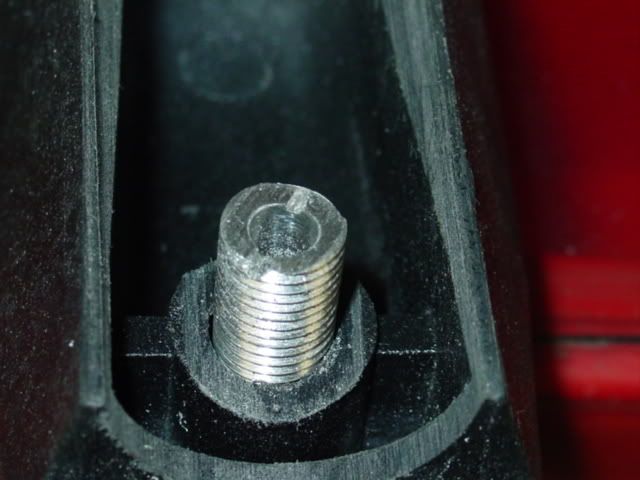
Put epoxy on the threads, set the studs a little high, and used the bar to "cove" the tops to match the barrel profile.
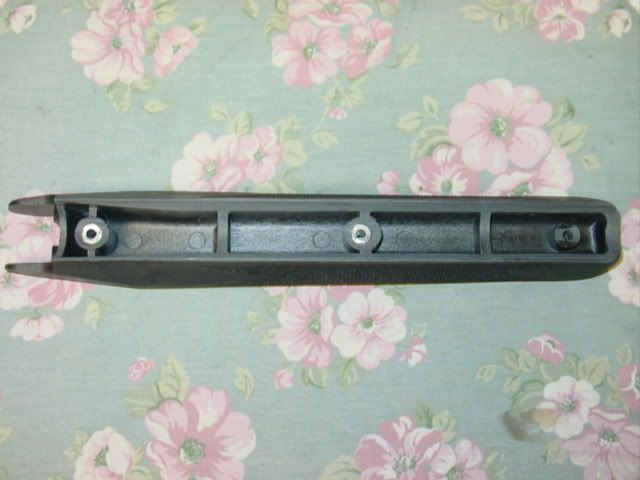
Ran out of "daylight" last night. will finish up by building dams of modeling clay in the hollow spaces to surround the pillars and fill with JB weld, clamp to the barrel to form a shoulder with the pillars in the center.