Omega
Well-Known Member
Ok, I am going to get a little controversial here.
Let me begin with this: I am a retired parachute rigger, school trained in sewing parachutes and other airborne and airdrop equipment. While at Ft Bragg, we were the first ones to make Riggers Belts (still called that) due to the drowning of some guys going through the Recondo course. Here at Ft Campbell, we made some of the first tie-ins for our guys that ride the pods on the MH-6 Little Birds, a piece of life saving equipment. Before I would agree to let my shop do this I had a certified lab do stress tests on the setup to make sure everything would hold as that is all that holds them onto the A/C.
Ok, now: What is this for? I know saddle hunting, but is it the tether, bridge, belt etc? Each piece takes different stresses, from static to dynamic. The tether, bridge and saddle take the most IMO, because if you happen to slip and fall, that would take extra G's, so depending on weight, distance etc, it can be considerable. The Lineman's belt, not so much, unless it get's caught up on a knot or limb on your way down.
Anyway, your method will work but you need a better sewing pattern, some of the big shops are making the same sewing pattern in their ropes, albeit with machines not by hand check the video to see how the machine makes three passes and duplicate that. This is one by Bluewater, a manufacturer of repelling ropes and equipment. Quality control, testing and things like quality of thread and tightness of the stitches come into play, that is why many are afraid to do stuff like this. It can be done, but hand stitching will probably not be as good as machine stitching.

A couple more suggestions if I may. First you are better off using a sewing awl to make stronger stitches, loose stiches weaken the bond, and allow nylon to nylon friction which also can weaken the loop, though it would take a long time. The picture and the linked one are different, I prefer the one in the link, though can't speak to the quality as I've had mine for many years.
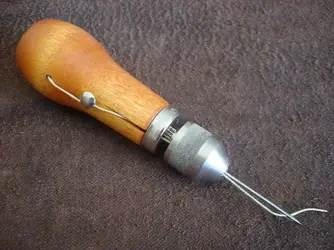
This allows lockstitches to be formed, so that if one stitch loop is compromised, the entire stitch won't let go, usually. Be sure to pull up on the stitch to form the loops as close to the middle as possible, again to lock the stitch with the material and undamaged loop if one or more surface stiches get damage, or internal ones for that matter.
As to the thread, we use size FF for many things, but upholstery thread would do just fine, it is very strong and should stand up to the wear and tear of outdoor use. The awl comes with some thread, but again, can't speak to it's strength and quality and this company makes very good quality thread.

Also, I would see about using some large shrink wrap along the stitch, to protect the thread from rubbing against the bark,

Also may look into possibly using another method, such as a loop splice (kind of like the Chinese finger trap), which is much much stronger, but that is for rope with a core, or coreless braided which kind of has a tube like structure, I don't know which kind you have so can't say either way.
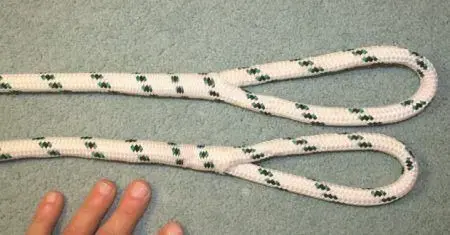
After saying all this, unless you have a bunch to do, or just like DIY, it may be better to just buy one, as they said, these companies are paid to make sure everything works and is safety tested, if not you family can sue the mess out of them. It may also get more expensive since you have to buy these things to do the work, and a one or two off project may not be worth it.
Let me begin with this: I am a retired parachute rigger, school trained in sewing parachutes and other airborne and airdrop equipment. While at Ft Bragg, we were the first ones to make Riggers Belts (still called that) due to the drowning of some guys going through the Recondo course. Here at Ft Campbell, we made some of the first tie-ins for our guys that ride the pods on the MH-6 Little Birds, a piece of life saving equipment. Before I would agree to let my shop do this I had a certified lab do stress tests on the setup to make sure everything would hold as that is all that holds them onto the A/C.
Ok, now: What is this for? I know saddle hunting, but is it the tether, bridge, belt etc? Each piece takes different stresses, from static to dynamic. The tether, bridge and saddle take the most IMO, because if you happen to slip and fall, that would take extra G's, so depending on weight, distance etc, it can be considerable. The Lineman's belt, not so much, unless it get's caught up on a knot or limb on your way down.
Anyway, your method will work but you need a better sewing pattern, some of the big shops are making the same sewing pattern in their ropes, albeit with machines not by hand check the video to see how the machine makes three passes and duplicate that. This is one by Bluewater, a manufacturer of repelling ropes and equipment. Quality control, testing and things like quality of thread and tightness of the stitches come into play, that is why many are afraid to do stuff like this. It can be done, but hand stitching will probably not be as good as machine stitching.
A couple more suggestions if I may. First you are better off using a sewing awl to make stronger stitches, loose stiches weaken the bond, and allow nylon to nylon friction which also can weaken the loop, though it would take a long time. The picture and the linked one are different, I prefer the one in the link, though can't speak to the quality as I've had mine for many years.
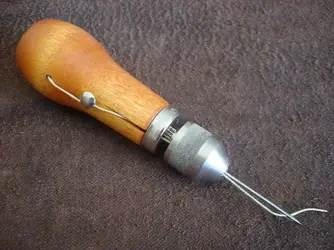
This allows lockstitches to be formed, so that if one stitch loop is compromised, the entire stitch won't let go, usually. Be sure to pull up on the stitch to form the loops as close to the middle as possible, again to lock the stitch with the material and undamaged loop if one or more surface stiches get damage, or internal ones for that matter.
As to the thread, we use size FF for many things, but upholstery thread would do just fine, it is very strong and should stand up to the wear and tear of outdoor use. The awl comes with some thread, but again, can't speak to it's strength and quality and this company makes very good quality thread.
Also, I would see about using some large shrink wrap along the stitch, to protect the thread from rubbing against the bark,
Also may look into possibly using another method, such as a loop splice (kind of like the Chinese finger trap), which is much much stronger, but that is for rope with a core, or coreless braided which kind of has a tube like structure, I don't know which kind you have so can't say either way.
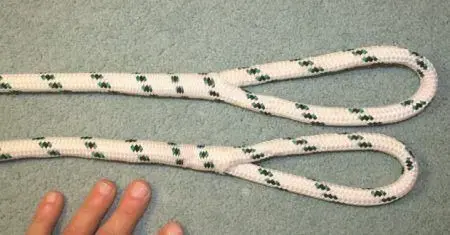
After saying all this, unless you have a bunch to do, or just like DIY, it may be better to just buy one, as they said, these companies are paid to make sure everything works and is safety tested, if not you family can sue the mess out of them. It may also get more expensive since you have to buy these things to do the work, and a one or two off project may not be worth it.